Automation and its effect on Labor in the Supply Chain
Automation vs Labor Costs
- share
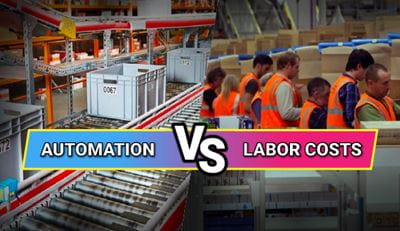
Associated University takes an in-depth look at the changing labor market in the supply chain industry and how automation can be applied to mitigate risks.
The US labor market has been quite a hot topic over the last two years, and in manufacturing and logistics sectors, the conversation is only getting started. Dramatic surges in consumer demand coupled with increasing difficulty in hiring talent have caused many Supply Chain companies quite the hardship, brought about by not just the pandemic, but by foreign trade qualms, domestic wage frustrations, ever-changing customer interests, and inconsistent material availability as well.
Here in the industrial automation corner of the market, we are currently witnessing unprecedented interest in industrial automation projects. Manufacturing and distribution companies are aggressively seeking automation solutions needed to offset vacant positions today, while also trying to make educated predictions about labor engagement conditions in the future. In many cases, companies are biting the bullet to head down the automation path sooner than they originally anticipated.
We take this as a sobering sign that the industry has already concluded what most of us suspect: general labor availability will continue to tighten, even in the face of increasing job creation, for the foreseeable future. In this article, we’ll share our thoughts on these shifting labor conditions, and then offer a framework of cost justifications that can help you structure automation projects in response.
Turning Fear into Strategies using Real Data
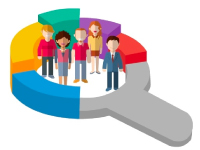
While many media outlets describe a shrinking labor force and lack of workers in the United States, we don’t find these to be technically accurate or useful beliefs for employers to hold. So, we turned to the Bureau of Labor Statistics to find high-level data that might shed some light on the current labor reality. What we found is an interestingly different situation - the workers are there, and the jobs are there, but for some reason, the two needs are no longer overlapping as they once did. Let’s look at several key data points:
-
Plenty of Jobs: The Bureau of Labor Statistics (BLS) predicts a 10% increase in overall Transportation and Warehousing industry employment by 2030.
-
The Workforce ‘is’ Accepting Material Handling Jobs, though at a Slowing Rate: Employment in the supply chain and logistics category has risen steadily since the early 2000s, even across both the global financial crisis of 2008 and the initial COVID pandemic of 2020. While the pandemic did stifle growth in nearly all industries briefly in early 2020 and again in early 2021, BLS Transportation and Warehousing industry data shows that the total employment volume has grown from 1.3 million employees in January 2020 to nearing 1.5 million employees in August 2021. In short, workers are accepting this type of work in non-trivial numbers, albeit at a slowing pace than in decades past.
-
Labor Competition, Not Labor Shrinkage:
If the positions are available and growing, why do we believe it to be shrinking? Let’s look at total population first. From 2010 to 2020, the US population increased by 23 million, and the active workforce grew by 7 million. While this 10-year growth does include a shrinkage of 3 million workers across 2020, the overall trend is upward. We often hear that the workforce is shrinking due to retirements and disinterested workers exiting the job market, but this is not strictly true. It is more accurate to say while the workforce is growing, available job numbers are also growing, and so the net result is that the job market is simply more competitive.
-
Bounce-Back Takes Time: It is very likely that we’re in the valley of a small retraction period as well, which we can exemplify against the financial crisis of the late 2010s. As then, people today may temporarily exit the workforce or be compelled towards part-time work to handle personal obligations, which is especially understandable given the health-centered motivators at hand these last two years. It will take several years for these affected workers to reallocate and come back to full-time positions.
-
US Workforce is Growing, But at a Slowing Rate: To further the above point, we find some suggestion in the data that capable workers are exiting the workforce by choice or by external obligation, not simply by exclusion. In the span from 2010 to 2020, BLS data shows a potentially adverse correlation between the increase in non-working workers and those workers claiming not to be looking for work – that today, when folks leave the standard workforce, they are more probable to leave for long periods of time, even permanently. While this workforce exit rate is growing in volume, the replacement rate of new workers is still higher, though slowing. This gives us another insight towards strategy: plan for even further competitive labor markets compounded by increasing exit proportions and decreasing rates of replacement.
-
Why are Workers (not) in Supply Chain and Logistics? : So far, we’ve established that we have an increasing US workforce, and though many new workers are indeed entering the material handling market, the rate of entry is clearly slowing. The remaining question is simply, why?
Aside from the country’s changing social perspectives on manufacturing and industrial work (slanting towards the negative, that is), a simple answer can be found in comparing the choices employees have when looking for equally-obtainable jobs of all types. BLS’ Wage Data may provide part of the answer: the average wage for warehouse laborers was $17.04 to $18.75 per hour in 2019 (intentionally using pre-pandemic data), which falls into the same range of wages as medical assistants, office support staff, and construction helpers.
Higher hourly wages approaching $25 per hour can be found in arguably similar (or in some cases, easier) jobs to both obtain and perform, such as general production staff, construction trade work, and maintenance work. Technology positions that need a small amount of specialized education and expertise, such as computer support and many medical, dental, or veterinary technician / technologist roles, push towards $30 per hour. Four-year degree roles in STEM and business fields exceed $30 per hour to start. Geography, population density, and other demographics all play a role as well.
In summary, if you’re a younger, lesser educated, or less experienced individual approaching the job market today, you have many more attractive opportunities either on par with or quickly exceeding material handling jobs that you’ll likely seek out first.
Forging a New Perspective on Labor Costs
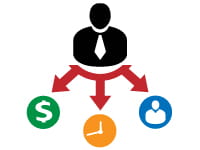
Our conclusion is that there is not a lack of workers in the labor force, nor an increasing number of workers systematically unavailable to the material handling market. Instead, there is a growing divergence between the job interests within the demographics of workers typically found in supply chain and logistics, and the work opportunities offered by employers in this space. This fundamentally changes employer’s perspective on - and reactions to - the current situation, in two ways:
-
In the short term, some stop-gap measures will be needed to maintain productivity in the face of extreme labor market volatility while workers return to the workforce and reorient themselves to their newfound needs. Tactics for such a change include temporary compensation programs, sharing labor pools across complementary businesses, and single-point automation solutions for specific work tasks.
-
In the long term, a paradigm shift in manual and semi-manual labor is needed, requiring employers to consider a consolidation of human capital into roles that are of interest to the emerging workforce, both in compensation and intrinsic value. Strategies to consider against this horizon can include cross-functional job designs, personnel management that measures human KPIs important to the employee, and system-level automation solutions that co-work with fewer, more specialized human workers.
We needn’t be fearful that the sky is falling, or that we have no place to turn in supplementing our workforce needs. While we can’t help with every economic and social aspect of the problem, we can certainly help on the automation front. From the above, we propose that automation is an exceptionally useful tool in your arsenal of options towards mitigating these labor market trends. The opportunity at hand is to reduce the burden of unfilled or under-filled positions with automated solutions, and to specifically consider such opportunities in terms of costs compared to human labor. For the rest of this article, we'll offer thoughts and justifications for implementing automated material handling systems to mitigate labor woes, specifically from a cost perspective.
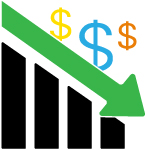
Cost Reduction
We’ll start our list of automation cost justifications with the typical go-to benefit: reduction of costs. These cost reductions can be found in a variety of forms, such as:
-
Fewer Employees Needed: Warehouse automation directly cuts the number of employees needed, reducing compensation costs. Consider not just the savings in raw compensation for positions automated away, but the future costs of recruiting that will surely increase as candidates steer their interests towards more attractive job types described above.
-
Increase Capacity: Production rates are improved by automation upgrades, allowing you to produce your required unit quantities in less time overall. Not only does this present the option to run your manufacturing line for less time, saving operating costs directly, but it also affords the opportunity to fill that saved time with additional orders, spreading out your operating costs over increased revenue, and reducing per-unit costs proportionally.
-
Continuous Process Improvement: Automation contributes to the further reduction of operating costs by way of improving processes and practices that otherwise were not available to improve prior. For example, launching an automated pick system for high-volume movers provides the opportunity to use this same equipment for automatic pick replenishment, as well as dynamic organization schemes that can automatically change as velocities change.
Cost Exchange
Many analysts would consider this category to be one of ‘cost avoidance’, however we prefer to take a different perspective. Automation entails a large upfront capital investment, followed by ongoing expenses related to the maintenance and upkeep of the new systems. If a project ROI works out correctly, these ongoing costs will be a lower dollar amount that the human-related costs that they replace over a certain number of years. But before we count the savings entirely as expense reduction, we suggest exchanging some of the savings for investment in tangent business areas that together can further improve the project’s ROI over time.
-
Ergonomics and Safety:
Replacing human operators in the most repetitive, non-ergonomic positions with automated systems insulates the company against injuries, workers' compensation claims, and lost time. Continue this improvement path by reinvesting a portion of insurance and worker’s comp premium savings into ergonomics and safety training, education, and certification.
-
Reduce Turnover and Maintenance Costs: The often-understated cost of employee turnover in supply chain teams will see a respectable ongoing cost avoidance after deploying automated solutions in the warehouse. Exchange some of these savings for additional training in your maintenance team, specifically around how to internally service a portion of the newly installed automated equipment, further avoiding a portion of external service costs.
-
Reduce Square Footage: In the case of evaluating automation in the construction of a new distribution or manufacturing facility, the cost exchange is typically as follows: increasing automation levels directly decreases the necessary warehouse square footage. This is a limited opportunity band however, as automation can quickly reach a point of diminishing returns. Exchange automation costs for square footage construction costs only up to the point that the project ROI is within expectations. You can apply the same savings for retrofit projects in existing spaces, so long as you have something viable to use the saved space for – otherwise, the space savings don’t have an assignable value.
Cost Reliability
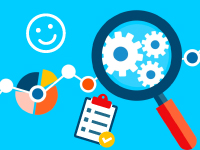
Referring back to the BLS data above, we remind readers again that it may be the safest bet to consider that current labor conditions are going to be around for some time. This leaves us with two perspectives on framing new projects: either charter automation projects as band-aids for current labor shortages, predicated on the assumption that ample labor will return in the near future, or instead charter projects as long-term solutions, assuming labor will continue to decrease in availability and increase in cost.
Isolating new employee entry into the marketplace by age from those leaving the workforce by age, the pandemic-induced symptoms would appear to only impact the new entry end of the equation, and workforce exit by retirement or aging out will inevitably remain. Given the choices and the data, it appears that choosing a long-term automation investment strategy is simply the most reliable, predictable, financially safe option.
-
Design Jobs for Lower Overall Talent Acquisition Costs: As job seekers veer away from lower paying, manual labor positions and look instead towards knowledge-based, higher-paying jobs, we might surmise that the type of workers we’ll be able to both find and attract in the future will be technicians and operators who can run automated systems, and not the manual laborers that the automation replaced. This reason alone may tell us that we should invest into automated systems simply as a strategy to fit into the upcoming labor market.
-
Machines Don’t Call-In Sick: Once automation is installed, we might be surprised at how operating costs begin to organically reduce in variation. Barring the expected service downtime, automated equipment tends to perform consistently, tirelessly, and exactly as expected. Compared to the variation that can come from an understaffed human workforce, automation presents a solution for reliable productivity.
-
Greater Flexibility at Lower Change Costs Equals Happier Customers: Our last topic towards justifying the cost of automation is a big-picture one, and this time we’ll take the vantage point of looking into your business through the eyes of your customers. Ultra-flexible, distribution is the direction that the industry is headed, generally speaking. Distributors who are able to reconfigure fulfillment systems around market swings ranging from seasonal consumer interests down to daily opportunistic sales are more attractive to their customers, hands down. More so, distribution centers that are able to redesign around SKU, vendor, packaging, density, lot, and unit changes are able to pick up more business. Automation brings a systematic, data-driven, software-enabled approach to solving for all these variables, and ultimately will make you a more reliable, adaptable, cost-consistent partner for your customers and end-users.
#industrialautomation #warehouseautomation #automationsystems #automatedmaterialhandling #warehouseautomationcompanies #advantagesofindustrialrobots