Data Integration: The Future of Labor Tracking and Management (Part 3)
How to Get Value out of a Labor Management System
- share
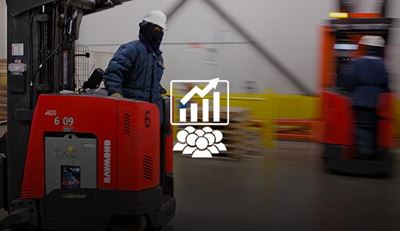
Warehouse managers know that increasing efficiency and productivity are key factors in overall profitability and success. But you may not know the extent to which data can help with making better decisions and improving your bottom line.
Warehouse managers know that increasing efficiency and productivity are key factors in overall profitability and success. But you may not know the extent to which data can help with making better decisions and improving your bottom line.
Tracking and measuring warehouse data can provide transformational insights on labor performance and can identify ways to best drive productivity and continuously improve.
In the previous two installments of this series, we defined data integration and examined ways to collect data. In this third installment of our four-part series, we’ll outline ways to use labor analytics to tell a more complete story and gain more value from your system.
Wrapping your head around “missing time”
Most managers want to ensure their team is highly utilized. Unfortunately, it’s customary to find a discrepancy between paid hours and total tracked hours – sometimes in excess of 60 to 90 minutes per day per employee.
In previous blogs, we discussed that while some of this time may be related to time-tracking errors, there are often instances where this time is truly unaccounted for. Using data to track work activity also gives you visibility into nonproductive time. Once you have full visibility into an employee’s activity, you can root out times when a teammate may be less active than desired/designed.
Although missing time can occur in large quantities, downtime is usually taking place several times a day for smaller periods of time, making it more difficult to identify. However, by analyzing data, you can identify those small increments of missing time to then achieve significant long-term savings and keep your warehouse accountable.
Indirect Activity
For many companies, 25% to 40% of a facility’s time is indirect time, or warehouse support time that isn’t directly involved in moving product in or out the door. As we’ve previously discussed, this activity usually isn’t captured in a warehouse management system and is omitted from traditional labor tracking. Although some of this activity is needed (box-making, housekeeping, etc.), it should be minimized to the level necessary to successfully run an operation.
The issue is that when an operation attempts to minimize missing or unaccounted for time, that time spent minimizing ends up being associated with additional indirect activity time. It’s up to the operation to minimize time spent on non-value-added tasks. Ask yourself: Do we need this much housekeeping? Did our working leads spend less-than-optimum time picking? Each individual task needs to be evaluated to determine the amount of labor necessary to properly complete the task. With a system that can track all time spent on labor, it’s easy to identify and optimize these activities and shift that activity toward value-added, product-moving tasks.
Driving Productivity
You might assume a labor management system would focus primarily on worker productivity, but the first priority is to address missing and indirect time. Once those obstacles are tackled, productivity can be driven through coaching, training, accountability, and incentive. Through these tactics, managers can remove barriers to increasing overall productivity and focus on maximizing employee utilization.
A labor management system can measure an employee’s utilization from a multivariable perspective. It considers the number of locations, sizes of boxes, amount of travel, etc., that an employee encounters in day-to-day work to accurately measure productivity. From there, you have an objective productivity standard for each employee and can fairly evaluate performance.
Continuous Improvement
You’ve minimized your missing time, minimized your indirect activity, and maximized your productivity — but potential savings don’t stop there. A labor management system that tracks overall operational performance can be used to measure and evaluate continuous improvement initiatives. If you perform a slotting exercise or a process improvement, you may see an uptick in productivity or a relative decrease in cost-to-serve/activity-based costing. This data can then prompt implementation of further changes and improvements in the overall system. With the help of this data-driven visibility, an operation can more easily identify inefficiencies and focus time and effort on refining processes.
In our next post, we’ll focus on continuous optimization — an integral step toward implementing intelligent solutions and getting the most out of your operation.
Data Integration Part 1 | Data Integration Part 2 | Data Integration Part 3