How to Better Utilize Facility Space with a Shuttle System
- share
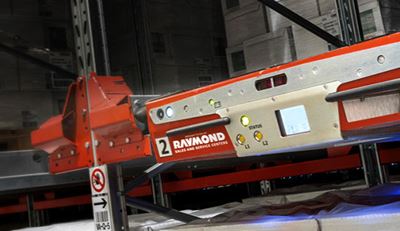
Finding ways to better utilize the available facility space is a constant challenge in distribution centers and manufacturing plants alike.
That is why high density material storage solutions have been sought for decades. Ultra-high density storage usually means low-tech rack like drive-in with its slow through-put rates and high fork truck damage, or pallet flow racks with limited lane depth. While on the other end of the spectrum is a fully automated AS/RS (Automated Storage & Retrieval System) with high capital cost and requisite high ceilings.
Fortunately, today there are technology-driven solutions to help you address this challenge and fill the void between these extremes.
A shuttle system is a very deep lane, medium-high speed, storage and retrieval solution that combines the labor and damage cost-savings benefits of semi-automation with the highest achievable storage density.
How It Works: A shuttle system consists of two parts; the storage structure and the shuttles, usually several shuttles per system. The storage structure is a self-supporting frame engineered to support loads up to 3,940 Lbs./pallet on a pair of parallel, horizontal rails similar to drive-in rack rails. This structure serves double duty as the track that the shuttles drive on as well as the support where the pallets rest. The second part is the working piece in the system. A fork truck picks up the shuttle as it would a pallet and then places it in the lane where put away or picking is to begin. Safety features include anti-skid pads and guide lights to help the driver pick the shuttle up correctly and a tilt sensor that will detect and sound an alarm if the shuttle starts to tip because it isn’t on the forks correctly. With the push of a single button on the remote control unit, the driver tells the shuttle to either pick pallets out or put them away. When putting pallets away, the shuttle waits patiently until it senses that the driver has put a pallet in the rack. Once detected, the shuttle automatically lifts the pallet up and carries it deep into the rack, where it places the load within an inch of any pallets already stored in that lane before returning back to the front of the lane for the next load. It’s just that easy. Pulling pallets out is simply the opposite process whereby the shuttle will continue to go into the rack and bring out loads as fast as the fork truck operator can take them away. The system can even improve count accuracy by counting out the correct number of pallets for the operator.
What is the best application?:
Maximized Storage Density: Shuttle systems provide the highest achievable storage density because it fills the available storage volume with a solid block of pallets. There are no length-wise aisles needed. The objective is to maximize the use of existing space thereby minimizing investment in new storage facilities.
Reduced Labor and Equipment Costs: The shuttle moves the pallets through the system autonomously while the fork truck operator moves the products to and from the system. Consider how much less time is spent driving fork trucks into and out of a rack system when there is a shuttle system there making those moves.
Key Opportunities for a Shuttle System: Operations with any of the following:
- A high pallet to SKU ratio.
- No more room for pallets on the floor.
- Using a 3PL (3rd Party Logistics) facility to store an overflow of pallets.
- A high cost of product and rack damage in existing drive-in/thru rack.
- A need for more dock turns per day.
- A desire to decrease the cost of fork truck maintenance and labor.
- Inefficient material movement in existing drive-in/thru system due to “honeycombing”.
- Interruptions due to pallets getting stuck in existing pallet flow systems and/or a need for deeper lanes than pallet flow can provide.
- A requirement to improve FIFO control
- Expensive climate-controlled storage environments needing better cubic storage utilization.
At the end of the day, the very deep, speedy and dense shuttle system is an excellent choice for appropriate applications that are looking to maximize their space.
To see a shuttle system in action go to this link: https://www.associated-solutions.com/products/storage-and-structures/pallet-storage/radio-shuttle
Radioshuttle