Data Integration: The Future of Labor Tracking and Management (Part 1)
The Future of Labor Tracking and Management
- share
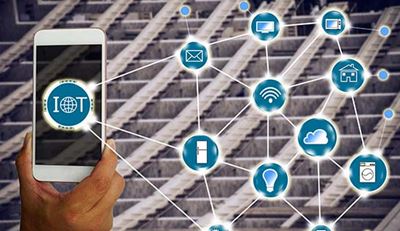
Labor costs are continually on the rise and every minute of every day is affecting your bottom line.
Labor costs are continually on the rise; this affects your bottom line. Meanwhile, customer service requirements continue to accelerate with more challenging value-added service demands. As managers, you are responsible for an overabundance of labor management processes, from recruiting and hiring to monitoring performance and progress.
Many companies have found tracking and managing their labor force to be challenging. While labor data is readily available, it often resides in multiple systems. In this series, we’re going to explore where labor management technology is going, the types of data available and how to effectively use data to manage your labor force.
Data tells a story
The historical methodology for looking at labor metrics has been to use warehouse management systems (WMS) or enterprise resource planning (ERP) information. However, as we look forward, hardware — whether it resides on forklifts, conveyors, semitrucks or other types of industrial equipment — is more frequently coming with embedded software.
In today’s world, data is king, so it is important to understand how to utilize it. First, you must understand where your baseline is and what steps you should be thinking about both in terms of specific technologies you want to adopt and take advantage of and the general mindset of how you plan for the future. The software is tracking and reporting some type of data. However, much of this data can be leveraged to tell a more complete story about your labor. Technology is rolling out faster and is becoming less expensive.
Labor, software, hardware, and automation not only coexist but also are actually interdependent because the combined data from all of these provides valuable information about where you are spending money, how your labor force is performing, and what decisions you should be making for the future.
Internet of things
The internet of things (IoT) is the concept of all systems around you creating data and tying all of it together. Many manufacturing systems were operated separately through a specific interface that was designed for that system. However, these systems are now integrated. Now, with systems that not only generate but also receive and share data, seizing the potential of these systems to drive smarter decision-making demands understanding how they all interconnect.
A distribution center also has a wide variety of data points coming from a multitude of systems. You might have time clocks, which are critical because they can be your benchmark for understanding what labor options are available, how many hours you are paying for, and how much you are spending on labor.
From there, we need to examine the other devices and systems you may have to ensure we understand what types of information you have access to and how data can be used to manage your labor force. Depending on how your facility is designed, these other systems may include telematics systems, ERP software and job coding, and/or other internal technologies.
No matter what systems you are using, when it comes to distribution, the IoT’s value lies not only in tying together the data that comes out of your systems but also in making sure you can retrieve that data so that you can get the right information to the right people. You need to be able to readily access all valuable data to derive meaningful benefits from it.
Most managers are evaluating what they should be doing in terms of labor tracking to find the best solution for their operation. Operations and systems are a little different, so finding the sweet spot based on the industry involved, the client base and labor needs is a process that everyone is working through.
Stay tuned for our next post, which will consider the different approaches to pulling in data and how creating a labor management system with multiple data sources is the way forward.
Data Integration Blog Series
Data Integration Part 1 | Data Integration Part 2 | Data Integration Part 3